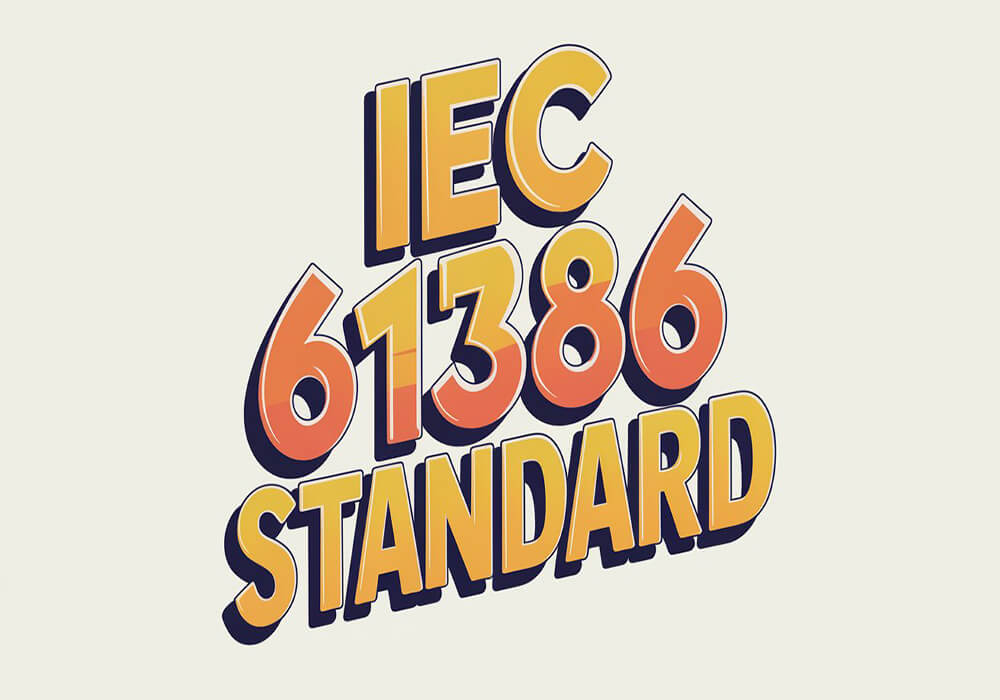
1 المقدمة
عند تركيب التمديدات الكهربائية، يُعد اختيار الأنابيب المناسبة أمرًا بالغ الأهمية لضمان السلامة والمتانة والأداء. من بين مواد الأنابيب المتنوعة المتاحة، تُعد أنابيب PVC (بولي فينيل كلوريد) خيارًا شائعًا بفضل مرونتها ومقاومتها للتآكل وسهولة تركيبها. يوفر معيار IEC 61386 إرشادات أساسية لتصنيف أنظمة الأنابيب ومتطلبات أدائها، مما يضمن استيفائها لمعايير السلامة والموثوقية العالمية.
سواء كنت تعمل في مشروع سكني أو تجاري أو صناعي، فإن فهم مواصفات ومزايا الأنابيب الكهربائية وفقًا لمعيار IEC 61386 أساسي لاتخاذ قرارات مدروسة. تتعمق هذه المقالة في تفاصيل أنظمة الأنابيب الكهربائية كما هو موضح في معيار IEC 61386، وتقارن أنابيب PVC بالأنابيب المعدنية التقليدية. نأمل أن تكون قد اكتسبت بنهاية هذا الدليل فهمًا شاملًا لتصنيفات الأنابيب الكهربائية، واختبارات الأداء، وأفضل الممارسات لاختيار النظام المناسب لمشاريعك الكهربائية.
لنبدأ بالعنوان في الفصل الأول، متبوعًا بشرح مفصل عن IEC ومعيار IEC 61386.
2. فهم معيار IEC وIEC 61386
2.1 ما هو IEC؟
اللجنة الكهروتقنية الدولية (IEC) هي منظمة عالمية معنية بإعداد ونشر المعايير الدولية لجميع التقنيات الكهربائية والإلكترونية والتقنيات ذات الصلة. تأسست اللجنة عام ١٩٠٦، وتلعب دورًا محوريًا في ضمان سلامة وجودة وتوافق المنتجات والأنظمة الكهربائية حول العالم. وتحظى معاييرها باعتماد واسع النطاق واعتراف الحكومات والمصنعين والهيئات التنظيمية، مما يعزز الاتساق الدولي في تصميم المنتجات الكهربائية وإنتاجها وأدائها.
من بين معاييرها المتنوعة، تلعب اللجنة الكهروتقنية الدولية (IEC) دورًا رائدًا في تطوير معايير أنظمة مثل أنظمة الأنابيب، وملحقات الأسلاك، والكابلات الكهربائية. وتتعاون المنظمة بشكل وثيق مع هيئات المعايير الوطنية، لضمان تطبيق معايير اللجنة الكهروتقنية الدولية عالميًا، مما يساعد الصناعات على الحفاظ على مستوى عالٍ من السلامة التشغيلية والتوافق الفني.
2.2 ما هو معيار IEC 61386؟
من بين معاييرها الرئيسية، تعتبر المواصفة IEC 61386 على نطاق واسع بمثابة المرجع المفضل لأنظمة القنوات، والتي تركز بشكل خاص على متطلبات التصنيف والأداء لأنظمة القنوات المستخدمة لحماية وتوجيه الأسلاك الكهربائية.
2.2.1 الدول والأسواق التي تعتمد معيار IEC 61386
الصين
قامت الصين بترجمة معيار IEC 61386 إلى المعيار الوطني GB/T 20041.1-2015، الذي يُنظّم أنظمة الأنابيب في السوق المحلية. يضمن هذا التعديل امتثال المصنّعين والمحترفين المحليين لمعايير السلامة والأداء المعترف بها دوليًا لأنظمة الأنابيب، مع مواءمتها مع متطلبات السوق العالمية.
الاتحاد الأوروبي
في الاتحاد الأوروبي، تتبنى دول مثل ألمانيا وفرنسا وغيرها معيار IEC 61386 على نطاق واسع من خلال علامة CE. يضمن هذا استيفاء أنظمة الأنابيب لمعايير السلامة والأداء الأوروبية الأساسية، مما يُسهّل حرية حركة البضائع بين الدول الأعضاء في الاتحاد الأوروبي. يساعد اعتراف الاتحاد الأوروبي بمعيار IEC 61386 المصنّعين والموردين على ضمان استيفاء منتجات الأنابيب الخاصة بهم لمتطلبات السوق الصارمة.
الدول الأعضاء الأخرى في اللجنة الكهروتقنية الدولية
غالبًا ما تستخدم أستراليا واليابان والعديد من الدول الأعضاء الأخرى في اللجنة الكهروتقنية الدولية (IEC) معيار IEC 61386 كأساس للوائحها الفنية الوطنية أو مواصفاتها الصناعية. قد تُكيّف هذه الدول معيار IEC 61386 ليناسب ظروفها المحلية بشكل أفضل، إلا أن المبادئ الأساسية لمعيار IEC 61386 تظل أساسًا لمتطلباتها الفنية. يُسهم الاعتماد الواسع لمعيار IEC 61386 في توحيد أنظمة الأنابيب، مما يضمن السلامة والجودة والتوافق عبر الحدود الدولية.
2.2.2 ما هي أنواع الأنابيب المذكورة في معيار IEC 61386؟
الأنابيب المعدنية - معروفة بقوتها الميكانيكية العالية وقدرتها على التأريض.
الأنابيب غير المعدنية - مصنوعة من مواد مثل PVC، والتي توفر مقاومة للتآكل والعزل الكهربائي.
الأنابيب المركبة - الجمع بين خصائص المواد المعدنية وغير المعدنية للتطبيقات المتخصصة.
يحدد هذا المعيار متطلبات الأداء في الظروف العادية والقاسية، بما في ذلك التعرض للضغط الميكانيكي والإجهاد الحراري والتعرض للمواد الكيميائية. كما يحدد أساليب الاختبار المستخدمة لتقييم مدى الامتثال لمعايير الأداء هذه.
بالإضافة إلى ذلك، يُقرّ المعيار IEC 61386 بأن بعض أنظمة التوصيلات الكهربائية قد تكون مناسبة للاستخدام في البيئات الخطرة. في مثل هذه الحالات، يجب استيفاء متطلبات إضافية لضمان السلامة والامتثال.
2.2.3 تصنيف الأنابيب وفقًا للمعيار IEC 61386
ينقسم IEC 61386 إلى عدة أجزاء، يتناول كل منها أنواعًا محددة من أنظمة الأنابيب ومتطلباتها الفريدة:
IEC 61386-21 - أنظمة الأنابيب الصلبة: تحدد متطلبات الأنابيب التي تحافظ على شكل ثابت تحت الضغط الميكانيكي.
IEC 61386-22 - أنظمة الأنابيب المرنة: تغطي الأنابيب التي يمكن ثنيها أو ثنيها دون العودة إلى شكلها الأصلي.
IEC 61386-23 - أنظمة الأنابيب المرنة: تحدد خصائص الأنابيب التي يمكن أن تنثني وتنحني بشكل متكرر دون حدوث أي ضرر.
IEC 61386-24 - أنظمة القنوات المدفونة تحت الأرض: تحدد المتطلبات الخاصة للقنوات المعرضة لضغط التربة والرطوبة وتغيرات درجات الحرارة.
IEC 61386-25 - أجهزة تثبيت الأنابيب: تحدد متطلبات الأداء للمكونات المستخدمة لتأمين أنظمة الأنابيب في مكانها.
يتيح نظام التصنيف هذا للمصنعين والمثبتين والمفتشين اختيار نظام التوصيل المناسب لتطبيقات محددة، مما يضمن الاتساق والامتثال لمعايير السلامة والأداء الدولية.
نقدم هنا بعض التفاصيل حول معيار IEC و IEC 61386.
في القسم التالي، سنلقي نظرة عن كثب على IEC 61386-1، وهو جزء أساسي من سلسلة IEC 61386 ويحدد المتطلبات العامة لأنظمة القنوات.
3. تقديم المتطلبات الرئيسية في معيار IEC 61386
يقدم المعيار IEC 61386-1 إرشادات مفصلة ومعايير أداء للأنابيب والتجهيزات المستخدمة لحماية وإدارة الموصلات والكابلات المعزولة في التركيبات الكهربائية أو أنظمة الاتصالات. صُممت هذه الأنظمة للاستخدام في بيئات ذات جهد كهربائي يصل إلى 1000 فولت تيار متردد و1500 فولت تيار مستمر، مما يجعلها مناسبة للتطبيقات السكنية والصناعية على حد سواء.
3.1 المتطلبات العامة وشروط الاختبار
نقدم هنا ملخصًا للمتطلبات العامة لأنظمة القنوات والظروف التي يتم اختبارها بموجبها.
3.1.1 المتطلبات العامة
التصميم والبناءيجب تصميم وتصنيع الأنابيب وتجهيزاتها لضمان أداء موثوق به في الاستخدام العادي. كما يجب أن توفر حماية كافية للمستخدم والمناطق المحيطة به.
التجميع والحماية:عند تجميعها وفقًا لتعليمات الشركة المصنعة، يجب أن توفر الأنابيب والتجهيزات حماية ميكانيكية، وحيثما يكون ذلك ضروريًا، حماية كهربائية للكابلات والموصلات الموجودة بالداخل.
سلامة المفاصل:يجب أن تتوافق أو تتجاوز الخصائص الوقائية للمفصل بين القناة وتركيبات القناة مستويات الحماية المعلنة لنظام القناة بأكمله.
متانة:يجب أن تتحمل الأنابيب والتجهيزات الضغوط التي تواجهها أثناء النقل والتخزين والتركيب والتطبيق المنتظم دون المساس بأدائها.
امتثال:يتم التحقق من الامتثال لهذه المتطلبات من خلال إجراء الاختبارات المحددة الموضحة في المعيار.
3.1.2 الشروط العامة للاختبارات
اختبارات النوعجميع الاختبارات التي تُجرى وفقًا للمعيار هي اختبارات نوعية. يجب اعتبار أنظمة الأنابيب من نفس التصنيف (مع اختلاف الألوان) من نفس نوع المنتج لأغراض الاختبار.
درجة الحرارة المحيطة:ما لم يُنص على خلاف ذلك، يجب إجراء الاختبارات عند درجة حرارة محيطة تبلغ 20 ± 5 درجة مئوية.
شروط العينةتُجرى الاختبارات عادةً على ثلاث عينات جديدة مأخوذة من طول واحد من الأنابيب. يجب تهيئة الأنابيب والوصلات غير المعدنية أو المركبة لمدة 240 ساعة على الأقل عند درجة حرارة 23 ± 2 درجة مئوية ورطوبة نسبية تتراوح بين 40 و60% قبل الاختبار.
حالة العيناتيجب أن تكون العينات نظيفة، وأن تكون جميع أجزائها مُركّبة كما هو الحال في الاستخدام العادي. يجب تجميع أنظمة الأنابيب وفقًا لتعليمات الشركة المُصنّعة، خاصةً عند الحاجة إلى قوة لتجميع الوصلات.
فشل الاختبار والإجراءاتفي حال عدم استيفاء عينة واحدة لمتطلبات الاختبار، تُجرى الاختبارات المتبقية على عينات إضافية حسب الحاجة. يستلزم الفشل في اختبار واحد إعادة اختبار جميع العينات بالكامل لضمان الامتثال.
3.2 معايير التصنيف وفقًا للمعيار IEC 61386
في معيار IEC 61386، تُصنّف أنظمة الأنابيب بناءً على خصائصها الميكانيكية والكهربائية ودرجة الحرارة والتأثيرات الخارجية ومقاومة اللهب. لا يتضمن هذا المعيار اختبارات فعلية، بل يُحدد كيفية تصنيف الأنابيب وفقًا لخصائص مُحددة. ولكن، في جوهره، يُساعد التصنيف المستخدمين على اختيار نوع الأنابيب المُناسب لتطبيقاتهم. نقدم هنا بعض التفاصيل لفهم أفضل.
3.2.1 الخصائص الميكانيكية
يتم تصنيف أنظمة القنوات وفقًا لقدرتها على تحمل الضغوط الميكانيكية المختلفة.
مقاومة الضغط:تتراوح من خفيف جدًا، وخفيف، ومتوسط، وثقيل، وثقيل جدًا.
مقاومة التأثير:يتم تصنيفها من خفيفة جدًا إلى ثقيلة جدًا، مما يشير إلى مدى قدرة القناة على التعامل مع الصدمات أو التأثيرات المادية.
مقاومة الانحناء:تتضمن التصنيفات: الصلبة، والمرنة، والقابلة للاستعادة الذاتية، والمرنة، والتي توضح مدى سهولة انحناء القناة أو عودتها إلى شكلها الأصلي.
قوة الشد:يتراوح من خفيف جدًا إلى ثقيل جدًا، مما يحدد قدرة المادة على مقاومة التمدد تحت الضغط.
سعة التحميل المعلقة:تشير التصنيفات من خفيف جدًا إلى ثقيل جدًا إلى مقدار الوزن الذي يمكن للقناة أن تتحمله عند تعليقها.
3.2.2 نطاقات درجات الحرارة
يتم تصنيف أنظمة القنوات بناءً على مقاومتها لدرجات الحرارة القصوى:
نطاق درجة الحرارة المنخفضة:التصنيفات من +5 درجة مئوية إلى -45 درجة مئوية، والتي تحدد الحد الأدنى لدرجة الحرارة التي يمكن عندها نقل القناة وتثبيتها واستخدامها.
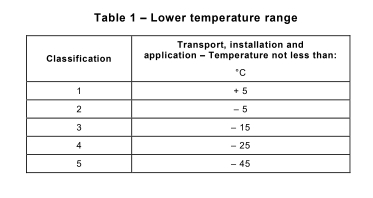
نطاق درجة الحرارة العليا:تتراوح التصنيفات من 60 درجة مئوية إلى 400 درجة مئوية، مما يشير إلى أقصى درجة حرارة يمكن أن يتحملها الأنبوب أثناء التطبيق والتركيب.
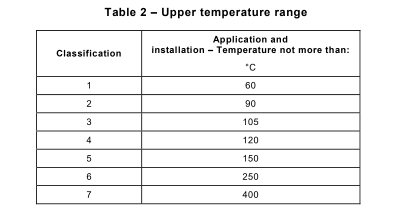
3.2.3 الخصائص الكهربائية
يجب أن تلبي أنظمة الأنابيب المتطلبات الكهربائية المحددة:
مع خصائص الاستمرارية الكهربائية:يضمن هذا التصنيف أن يحافظ الأنبوب على استمرارية الكهرباء، مما يوفر التأريض والحماية.
مع خصائص العزل الكهربائي: يشير إلى قدرة القناة على العمل كعازل، مما يمنع مرور التيار الكهربائي من خلاله.
3.2.4 مقاومة التأثيرات الخارجية
يتم تصنيف قدرة القناة على تحمل العوامل البيئية الخارجية على النحو التالي:
الحماية من دخول الأجسام الصلبة:يتم تحديد مستوى الحماية وفقًا لمعايير IEC 60529، مع حماية IP3X على الأقل.
الحماية من دخول المياه:تعتمد التصنيفات على القدرة على منع دخول الماء إلى القناة، مع تصنيف IPX0 على الأقل.
مقاومة التآكل:يمكن تصنيف القنوات مع أو بدون حماية ضد التآكل، اعتمادًا على المادة والاستخدام المقصود.
3.2.5 انتشار اللهب
يتم تصنيف أنظمة القنوات حسب مقاومتها لانتشار اللهب:
غير قابل للتكاثر عن طريق اللهب:قناة لا تسمح بانتشار النيران على طولها.
انتشار اللهب:قناة قد تسمح بانتشار اللهب، على الرغم من أنها تقاوم النار إلى حد ما.
بالإضافة إلى ذلك، في بلدان مثل أستراليا والنمسا، يمكن تصنيف القنوات على أنها منخفضة الانبعاثات الغازية الحمضية، مما يشير إلى قدرتها على تحمل بعض المخاطر البيئية.
3.3 متطلبات العلامات والتوثيق
هنا نقوم أيضًا بتلخيص متطلبات وضع العلامات في IEC 61386. إن فهم متطلبات وضع العلامات والتوثيق لأنظمة الأنابيب أمر ضروري لكل من الموردين والعملاء.
للموردين، فهو يضمن الامتثال للمعايير الدولية، ويحسن إمكانية التتبع، ويبني سمعة العلامة التجارية من خلال توفير هوية واضحة للمنتج ومعلومات موثوقة.
للعملاءيضمن هذا حصولهم على منتجات عالية الجودة تلبي معايير الأداء المحددة، ويساعد في اختيار المنتج المناسب، ويضمن سهولة التركيب والدعم. يُسهّل وضع العلامات المناسبة إتمام المعاملات بسلاسة، ويعزز الثقة في سلامة المنتجات وموثوقيتها.
هوية الشركة المصنعة:يجب أن يتم وضع علامة على كل مجرى باسم الشركة المصنعة أو البائع المسؤول أو العلامة التجارية وعلامة تعريف المنتج (على سبيل المثال، رقم الكتالوج أو الرمز) لسهولة التعرف عليه.
رمز التصنيفيجب وضع رمز تصنيف على الأنبوب أو أصغر عبوة مُرفقة به. يجب أن يتضمن هذا الرمز، وفقًا للملحق أ، الأرقام الأربعة الأولى على الأقل، وأن يكون واضحًا.
قنوات الاسترداد الذاتي:يجب أن تحمل الأنابيب ذاتية الاسترداد أيضًا رمز التصنيف على الأنبوب أو أصغر حزمة مقدمة، مع ملصق واضح يظهر الأرقام الخمسة الأولى على الأقل.
التوافق والتصنيف:يعتبر المصنع مسؤولاً عن الإشارة إلى توافق الأجزاء داخل نظام الأنابيب ويجب عليه توفير التصنيف الكامل في مطبوعات المنتج، بالإضافة إلى المعلومات الضرورية للنقل والتخزين والتركيب والاستخدام المناسبين.
انتشار اللهبيجب وضع رمز خاص (رمز اللهب) على الأنابيب المصنوعة من مواد ناقلة للهب بطولها الكامل، ويفضل ألا تتجاوز المسافة بين كل أنبوب والآخر مترًا واحدًا. إذا كانت العبوة تمنع ظهور العلامة، فيجب وضعها على العبوة.
مرافق التأريض:يجب وضع علامة IEC 60417-5019 على الأنابيب التي تحتوي على مرافق تأريض للتأريض الواقي، ولكن لا ينبغي وضع هذا الرمز على الأجزاء القابلة للإزالة مثل التركيبات.
المتانة والوضوحيجب أن تكون العلامات متينة وواضحة وقابلة للقراءة، ويمكن فحصها من خلال الرؤية الطبيعية أو المصححة. كما يجب أن يخضع سطح العلامة لاختبارات احتكاك لضمان متانته، مع اتباع إجراءات محددة لاختبار تحمل العلامات في ظل ظروف مختلفة.
الامتثال للتفتيشيجب فحص جميع العلامات للتأكد من مطابقتها للمعايير المحددة. يشمل ذلك فحصًا بصريًا واختبارات فرك بقطعة قطن مغموسة في مذيبات مثل n-hexane 95%، لضمان سلامتها في ظل الاستخدام العادي والتآكل.
3.4 أبعاد ومتطلبات البناء لأنظمة الأنابيب
إن فهم أبعاد ومتطلبات بناء أنظمة الأنابيب أمر بالغ الأهمية لضمان التركيب الآمن والأداء الموثوق به.
3.4.1 الامتثال للأبعاد
الخيوط والأقطار الخارجية: يجب أن تتوافق خيوط الأنابيب والأقطار الخارجية مع معايير IEC 60423. هذا يضمن اتساق جميع أحجام الخيوط وأقطارها، واستيفائها للمواصفات اللازمة للتوافق والسلامة.
الأبعاد الأخرى: بالنسبة لجميع الأبعاد الأخرى، يجب أن تلبي أنظمة القنوات المتطلبات الموضحة في الجزء 2 من IEC 61386، مما يضمن الاتساق والقياسات الموحدة عبر أنواع مختلفة من أنظمة القنوات.
3.4.2 معايير البناء
الحواف الحادة والنتوءات: يجب تصميم وإنشاء أنظمة الأنابيب بدون حواف حادة أو نتوءات أو نتوءات سطحية يمكن أن تتسبب في تلف الكابلات أو إلحاق الضرر بالمثبتين والمستخدمين أثناء التعامل والتركيب.
براغي:يجب أن تتوافق البراغي المستخدمة في تثبيت المكونات أو الأغطية مع إرشادات محددة:
- خيوط مترية ISO:يجب أن تستخدم جميع البراغي خيوطًا مترية وفقًا للمعايير الدولية لمنع تلف عزل الكابل أثناء التثبيت.
- براغي قطع الخيوط:لا ينبغي استخدام مسامير قطع الخيوط لتجنب إتلاف الأنابيب أو التركيبات.
تثبيت البراغي وعزم الدورانيجب أن تكون براغي تثبيت أجزاء الأنابيب قادرة على تحمل الضغوط الميكانيكية أثناء التركيب والاستخدام العادي. للتثبيت باستخدام براغي لولبية مُشكَّلة مسبقًا، يجب شد البراغي وفكها 10 مرات (أو 5 مرات في حالات خاصة) دون تعرضها للتلف. يجب اختبار براغي التشكيل اللولبي لقيم عزم الدوران كما هو موضح في الجدول 3، لضمان التركيب السليم والمتانة دون إتلاف البرغي أو الجزء اللولبي.
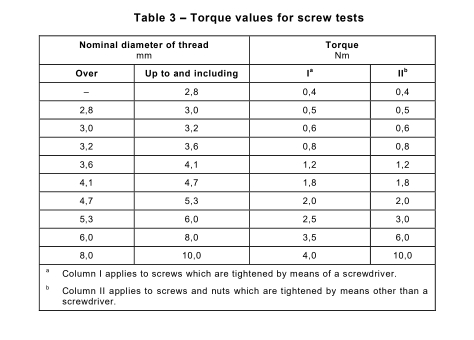
المادة والمقاومةيجب أن توفر أي مادة داخل المفصل (مثل المطاط والألياف) المعرضة للتأثيرات الخارجية نفس مستوى الحماية الذي توفره الأنابيب أو التركيبات نفسها. وهذا يضمن مقاومة النظام الشاملة للعوامل البيئية.
التفكيكبالنسبة لأنظمة الأنابيب المجمعة بدون خيوط، يجب على الشركات المصنعة تحديد ما إذا كان من الممكن تفكيك النظام وكيف يمكن القيام بذلك بأمان، مع ضمان سهولة الصيانة والمرونة.
4. الاختبارات التفصيلية للأنابيب وفقًا لمعيار IEC 61386
4.1 الخصائص الميكانيكية المطلوبة في IEC 61386
يجب أن تتمتع أنظمة الأنابيب بمتانة ميكانيكية كافية لتحمل القوى التي تتعرض لها أثناء الاستخدام. يجب ألا تتعرض هذه الأنظمة، حسب تصنيفها، للتشقق أو التشوه لدرجة يصعب معها إدخال الموصلات أو الكابلات المعزولة. كما يجب أن تكون قادرة على دعم المعدات عند استخدامها كقواعد، سواءً أثناء التركيب أو التشغيل. يجب التحقق من كفاءتها من خلال الاختبارات التالية. لذا، سنقدم فيما يلي شرحًا مفصلاً لهذه الاختبارات.
من أجل فهم أفضل، ما لم يتم تحديد خلاف ذلك، فإن الاختبارات ذات الصلة المذكورة أدناه مطلوبة عادةً لجميع أنواع الأنابيب الكهربائية، بما في ذلك الأنابيب المعدنية وغير المعدنية والمركبة.
4.1.1 اختبار الضغط
تُختبر عينات من الأنابيب (بطول 200 ± 5 مم) للضغط بتطبيق قوة متزايدة تدريجيًا، حتى تصل إلى القيمة المحددة لكل تصنيف من تصنيفات الأنابيب. بعد تطبيق القوة، يُقاس القطر الخارجي للعينة مرة أخرى للتحقق من أي تشوه. يجب ألا يتجاوز الفرق بين القطر الابتدائي والقطر المسطح 25% من البعد الأصلي. تُزال القوة بعد ذلك، وتُفحص العينة بحثًا عن أي شقوق. يضمن هذا الاختبار قدرة الأنابيب على تحمل الضغط أثناء التركيب والاستخدام.
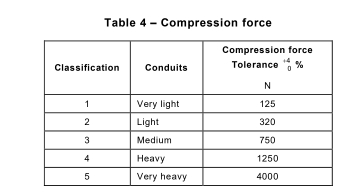
4.1.2 اختبار التأثير
يُقيّم هذا الاختبار مقاومة أنظمة الأنابيب للصدمات من خلال تعريض اثنتي عشرة عينة (بطول 200 ± 5 مم) لصدمة محددة. تُهيأ العينات أولًا عند درجة الحرارة المطلوبة، ثم تُسقط مطرقة على العينة لمحاكاة الصدمات المحتملة في الواقع. تختلف كتلة المطرقة وارتفاع السقوط باختلاف تصنيف الأنابيب، حيث تتطلب الفئات الأثقل اختبارات صدمات أكثر دقة. بعد الاختبار، يجب ألا يُظهر الأنبوب أي ضرر أو تشققات أو تشوهات تُذكر.
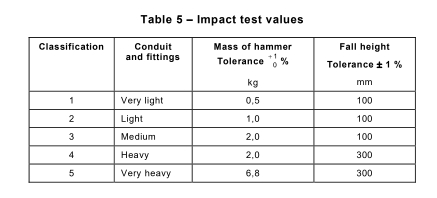
4.1.3 اختبار الانحناء
يتم إجراء اختبار الانحناء للتأكد من أن الأنابيب المعدنية وغير المعدنية يمكنها تحمل الانحناء أثناء التثبيت دون حدوث أي ضرر.
للأنابيب المعدنية (الأحجام 16 و20 و25)تُثنى العينات بزاوية 90° ± 5° بنصف قطر داخلي يصل إلى ستة أضعاف القطر الاسمي. بعد الثني، يجب ألا تظهر على الأنبوب أي شقوق أو فتحات أو تشوهات زائدة، ويجب أن تبقى اللحامات سليمة. بالنسبة للأنابيب ذات اللحامات الملحومة، يُختبر كلا جانبي الانحناء لضمان سلامة الأنبوب من الناحية الهيكلية.
للأنابيب غير المعدنيةعملية الثني مماثلة، بطول ٥٠٠ مم ± ١٠ مم، وتُجرى عند درجة حرارة ١٢ ± ٢ درجة مئوية. يجب ألا تُظهر هذه العينات أي ضرر مرئي، كالتشققات أو التشوهات، بعد الاختبار. يجب أن يكون الأنبوب قادرًا على العودة إلى شكله المستقيم تحت تأثير وزنه دون الحاجة إلى أي سرعة ابتدائية.
للأنابيب المركبة، تم إعلانها من قبل الشركة المصنعة بأنها قابلة للانحناء وتم اختبارها كأنابيب معدنية وغير معدنية.
4.1.4 اختبار المرونة
يُجرى اختبار الانحناء لضمان قدرة أنظمة الأنابيب، وخاصةً الأنابيب المرنة، على تحمل الحركة المتكررة دون أي ضرر. يُجرى الاختبار على ست عينات، ثلاث منها تُختبر عند الحد الأدنى من درجات الحرارة المُعلنة، وثلاث أخرى عند الحد الأقصى لها، وذلك لأغراض النقل والتطبيق والتركيب.
بالنسبة للأنابيب المرنة، يضمن الاختبار ملاءمة المنتج للنقل والتركيب في درجات الحرارة المحيطة والقصوى وفقًا لمواصفات الشركة المصنعة. إذا كانت الأنابيب مناسبة فقط للانحناء في درجة الحرارة المحيطة، يُجرى الاختبار عند درجة حرارة 20 ± 2 درجة مئوية.
تُثبّت العينات على دعامة متذبذبة، وتُعرّض لحركة ذهابًا وإيابًا بتردد 5000 انثناءة بزاوية 180 درجة. يُجرى الاختبار بسرعة 40 ± 5 انثناءات في الدقيقة. بعد اكتمال دورة الانثناء، يجب ألا تُظهر العينات أي شقوق أو تلف واضح في الرؤية الطبيعية أو المصححة، مما يؤكد متانة الأنبوب تحت الحركة المتكررة.
يضمن هذا الاختبار أن تحافظ الأنابيب المرنة على سلامتها أثناء التركيب والتداول، مما يجعلها مناسبة للبيئات التي تتطلب الحركة المتكررة أو الانحناء.
4.1.5 اختبار الانهيار
يُقيّم اختبار الانهيار قدرة الأنابيب غير المعدنية والمركبة على تحمّل الضغوط الخارجية دون تشوّه أو انهيار. ولا تخضع الأنابيب المعدنية لهذا الاختبار.
بالنسبة للأنابيب غير المعدنية، والتي تُصنّفها الشركة المصنعة على أنها قابلة للثني، تُثنى العينات ثم تُثبّت على دعامة صلبة باستخدام أربعة أحزمة، كما هو موضح في تعليمات الشركة المصنعة. ثم تُوضع العينات في خزانة تسخين بدرجة حرارة محددة لمدة ٢٤ ± ١٥ دقيقة لتهيئتها بشكل صحيح. بعد هذه الفترة، يُثبّت الأنبوب بحيث تكون الأجزاء المستقيمة من العينة بزاوية ٤٥ درجة مع العمودي، مما يضمن ثباتها عند تعرضها لقوى خارجية.
يضمن هذا الاختبار قدرة الأنبوب على تحمل الضغط دون انهيار أو تشوه، مع الحفاظ على قدرته على حماية الكابلات بداخله. يُعد هذا الاختبار ضروريًا للمواد غير المعدنية والمركبة لضمان متانتها في ظروف الاستخدام العادية.
4.1.6 اختبار الشد
يُجرى اختبار الشد لقياس قوة شد أنظمة الأنابيب. تُجمع عينة مكونة من أنبوب ووصلتين (أو وصلات طرفية) وفقًا لتعليمات الشركة المصنعة، مع التأكد من أن طول الأنبوب بين الوصلات لا يقل عن 200 مم. إذا تعذر تحقيق هذا الطول، يُجرى الاختبار على عينتين من الأنابيب والوصلات.
يُطبّق الاختبار قوة شد متزايدة بانتظام حتى تصل إلى القيمة المحددة في الجدول 6. تُحافظ على هذه القوة لمدة دقيقتين ± 10 ثوانٍ عند درجة حرارة 23 ± 2 درجة مئوية. بعد الاختبار، يجب أن تبقى الأنابيب والتجهيزات مُركّبة بشكل صحيح، دون أي ضرر واضح للمكونات عند ملاحظتها دون تكبير.
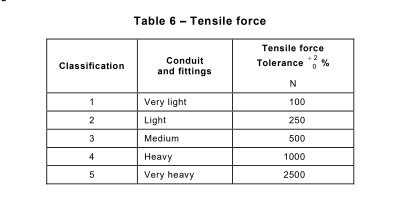
إذا لم يتم الإعلان عن قوة الشد للنظام، فيجب على الشركة المصنعة التأكد من أن النظام يلبي
معايير قوة الشد ذات الصلة وفقًا للجزء ذي الصلة من معيار IEC 61386. يضمن هذا الاختبار حفاظ النظام على سلامته الهيكلية أثناء الاستخدام دون إتلاف التركيبات أو الأنابيب تحت تأثير قوة الشد.
4.1.7 اختبار الحمل المعلق
يُقيّم اختبار الحمل المُعلّق قوة ومتانة وصلات الأنابيب المُصمّمة لدعم الأحمال المُعلّقة. تُثبّت الوصلة على هيكل صلب باستخدام طريقة مُعتمدة من المُصنّع، بحيث يكون مُوجّهًا نحو الأسفل. يُطبّق حمل مُحدّد، بناءً على التصنيف الوارد في الجدول 7، لمدة 48 ساعة.
لاجتياز الاختبار، يجب ألا تظهر على التركيبة أي شقوق أو تشوهات ظاهرة قد تؤثر على استخدامها الطبيعي. بالنسبة لتركيبات الأنابيب غير المعدنية والمركبة، يُجرى الاختبار في خزانة تسخين عند أقصى درجة حرارة تشغيل مُعلنة، مع تفاوت قدره ±2 درجة مئوية.
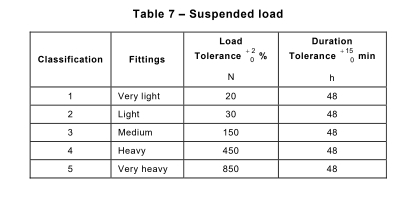
4.2 الخصائص الكهربائية
4.2.1 المتطلبات الكهربائية
اختبار الاستمرارية (المعدنية والمركبة): يجب اختبار أنظمة الأنابيب التي تعلن عن خصائص الاستمرارية الكهربائية فورًا بعد التثبيت.
ربط الأجزاء المعدنية (المعدنية، المركبة): يجب تصميم أنابيب معدنية أو مركبة تسمح بربط الأجزاء المعدنية التي يسهل الوصول إليها. يتم التحقق من الامتثال عن طريق التفتيش.
التأريض (المعدني، المركب): يجب تأريض الأجزاء الموصلة من الأنابيب المعدنية أو المركبة، والتي قد تصبح نشطة في حالة حدوث عطل، بشكل صحيح. يتم اختبار التوافق عن طريق الترابط.
قوة العزل (غير المعدنية، المركبة): يجب أن تتمتع أنظمة الأنابيب غير المعدنية والمركبة بمقاومة عزل وقوة عزل كهربائي كافية. يُختبر التوافق من خلال اختبارات القوة العازلة ومقاومة العزل.
4.2.2 اختبار الترابط (المعدني، المركب)
لتقييم الاستمرارية الكهربائية لأنظمة الأنابيب المعدنية والمركبة، يُجرى اختبار الترابط بتوصيل 10 قطع أنابيب بالوصلات وفقًا لتعليمات الشركة المصنعة. يُمرر تيار كهربائي شدته 25 أمبير بتردد 50-60 هرتز عبر النظام لمدة 60 ثانية، مع قياس انخفاض الجهد لحساب المقاومة. يجب ألا تتجاوز المقاومة 0.1 أوم لضمان الترابط الكهربائي السليم. في حال استخدام أنواع مختلفة من الوصلات، يجب تكرار الاختبار لكل نوع. بالإضافة إلى ذلك، يجب إزالة أي طبقات واقية قد تؤثر على التوصيل قبل الاختبار.
4.2.3 القوة العازلة ومقاومة العزل (غير المعدنية، المركبة)
بالنسبة لأنظمة الأنابيب غير المعدنية والمركبة، تُختبر قوة العزل بغمر العينات في محلول ملحي. بعد النقع، يُجرى اختبار جهد عالي بزيادة الجهد تدريجيًا إلى 2000 فولت تيار متردد على مدار 15 دقيقة، مع الحفاظ عليه لمدة 5 ثوانٍ. يُعتبر النظام متوافقًا إذا تحمل هذا الجهد دون تعطل دائرة أمان 100 مللي أمبير. تُقاس مقاومة العزل أيضًا بعد تطبيق الجهد، ويجب أن يُظهر النظام مقاومة لا تقل عن 100 ميجا أوم لاجتياز الاختبار.
تخضع تجهيزات الأنابيب لإجراءات اختبار مماثلة. تُغمر العينات في الماء لمدة ٢٤ ساعة، ثم تُجفف قبل الاختبار. تُغلّف التجهيزات بمادة عازلة، ويُدخل قطب كهربائي لمحاكاة ظروف التركيب الحقيقية. بعد اختبار الجهد العالي، يجب أن تكون مقاومة العزل أكبر من ٥ ميجا أوم لتكون مطابقة للمواصفات.
4.3 الخصائص الحرارية
يجب أن تُظهِر الأنابيب غير المعدنية والمركبة مقاومةً حراريةً كافية. ويُحدَّد الامتثال من خلال إجراءات اختبار موحدة. لم يُذكر الأنابيب المعدنية صراحةً في هذا القسم، إذ عادةً ما تختلف معايير الأداء الحراري للمعدن.
يُجرى اختبار التسخين وفقًا لتصنيف معدل الضغط المُعلن للأنبوب. تُسخّن عينات من الأنبوب (كل منها ١٠٠ ± ٥ مم) لمدة ٤ ساعات و٥ دقائق عند درجة الحرارة المحددة (انظر الجدول ٨) مع تفاوت قدره ± ٢ درجة مئوية.
بعد التسخين، يُطبّق حمل لمدة ٢٤ ساعة و١٥ دقيقة باستخدام قضيب فولاذي بقطر ٦.٠ ± ٠.١ مم، موضوع عموديًا على محور الأنبوب. يتوافق الحمل الإجمالي المطبّق مع التصنيف الوارد في الجدول ٨، مما يضمن محاكاة دقيقة للإجهاد الميكانيكي.
بعد إزالة الحمل، يجب أن يسمح الأنبوب بمرور مقياس مناسب الحجم تحت تأثير وزنه دون أي قوة خارجية. يضمن هذا الاختبار احتفاظ الأنبوب بأبعاده الداخلية وسلامته الهيكلية بعد التعرض للإجهاد الحراري والميكانيكي.
4.4 مخاطر الحرائق
تخضع الأنابيب غير المعدنية والمركبة لجميع اختبارات مخاطر الحرائق، بما في ذلك تقييمات استخدام الأسلاك المتوهجة واللهب، لضمان استيفائها لمعايير مقاومة الحرائق. لا يُذكر استخدام الأنابيب المعدنية صراحةً في معايير الاختبار.
4.4.1 رد الفعل تجاه النار
لا تتلامس أنظمة الأنابيب مباشرةً مع الأجزاء الحية، مما يعني أنها لا تُشكل خطرًا مباشرًا لاندلاع الحرائق. مع ذلك، يجب تقييم مساهمتها في انتشار الحرائق واللهب، خاصةً في تجهيزات الأنابيب غير المعدنية والمركبة.
4.4.2 المساهمة في الحريق
يجب أن تتمتع أنظمة الأنابيب غير القابلة لانتشار اللهب بمقاومة كافية لانتشار اللهب. يُقيّم توافق تجهيزات الأنابيب غير المعدنية والمركبة من خلال اختبارين رئيسيين. الأول هو اختبار السلك المتوهج، الذي يُجرى وفقًا للمعيار IEC 60695-2-11، حيث يُوضع سلك مُسخّن عند درجة حرارة 750 درجة مئوية على الأنبوب في وضع رأسي. يُجتاز الأنبوب الاختبار إذا لم يُظهر أي لهب مرئي أو توهج مستمر، أو إذا انطفأ أي لهب خلال 30 ثانية بعد إزالة السلك.
الاختبار الثاني يُطبّق لهبًا بقوة 1 كيلوواط، وفقًا للمعيار IEC 60695-11-2. تُوضع عينة الأنبوب عموديًا داخل غلاف معدني ذي وجه مفتوح لتقليل تداخل الهواء الخارجي. يُقيّم هذا الاختبار أيضًا مقاومة الأنابيب غير المعدنية والمركبة للهب عند التعرض المباشر للنيران.
4.4.3 انتشار الحريق
لضمان مقاومة الحريق، تُختبر الأنابيب عن طريق التعرض المباشر للهب بزاوية 45 درجة داخل غلاف معدني مُحكم. تُثبّت العينات بإحكام باستخدام مشابك لمنع التشوه أثناء الاختبار. يوفر قضيب فولاذي دعمًا إضافيًا للأنابيب الرقيقة. يختلف زمن التعرض للهب باختلاف سُمك المادة، كما هو موضح في الجدول 9، حيث يتراوح بين 20 ثانية للأنابيب بسمك 0.5 مم و500 ثانية للأنابيب التي يصل سُمكها إلى 8 مم.
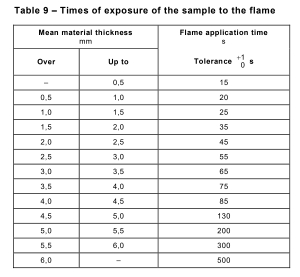
يُعتبر الأنبوب ناجحًا إذا لم يشتعل، أو إذا انطفأ ذاتيًا خلال 30 ثانية بعد إزالة اللهب. بالإضافة إلى ذلك، يضمن الاختبار عدم اشتعال منديل ورقي موضوع أسفل الأنبوب، وعدم وجود تفحم أو احتراق يمتد لأكثر من 50 مم من نقطة التعرض للهب. تضمن هذه المعايير استيفاء الأنابيب غير المعدنية لمعايير السلامة من الحرائق، مما يمنع انتشار اللهب في التركيبات الكهربائية.
4.4.4 خصائص إضافية لتفاعلات النار
في بعض المناطق، يجب أن تتوافق الأنابيب غير المعدنية أيضًا مع معايير انبعاث الغازات الحمضية المنخفضة.
في أستراليايتم اختبار الأنابيب المصنفة على أنها ذات انبعاثات غازية منخفضة الحمض وفقًا للمعيار IEC 60754-1، حيث يجب ألا تتجاوز الانبعاثات 5 ملغ من حمض الهيدروكلوريك لكل جرام من المادة.
في النمساتنطبق لوائح مماثلة بموجب المعيار IEC 60754-2. تساعد هذه المتطلبات على تقليل انبعاثات الغازات السامة في حالة نشوب حريق، مما يُحسّن السلامة في البيئات المغلقة.
4.5 التأثيرات الخارجية
تنطبق حماية العلبة على المواد غير المعدنية والمعدنية، ولكن مقاومة التآكل والاختبار تركز على الأنظمة المعدنية، في حين أن المواد غير المعدنية لا يتم اختبارها بشكل صريح، إلا أنها في بعض الأحيان تتمتع بمقاومة متأصلة للمواد الكيميائية.
4.5.1 درجة الحماية التي يوفرها الغلاف
يجب أن توفر أنظمة الأنابيب مقاومة كافية للتأثيرات الخارجية، وفقًا للتصنيف المُعلن من قِبل المُصنِّع، مع حد أدنى من معيار IP30. ويتم التحقق من الامتثال من خلال اختبارات مُحددة لتقييم الحماية من الأجسام الصلبة وتسرب المياه.
الحماية من الأجسام الصلبة الغريبةتُختبر التجميعات المصنوعة من الأنابيب والتجهيزات لضمان عدم دخول الغبار بشكل مرئي في ظروف الرؤية الطبيعية. تتبع الاختبارات معايير IEC 60529، وتُعتبر الأنظمة التي تحصل على الرقمين 5 أو 6 متوافقة.
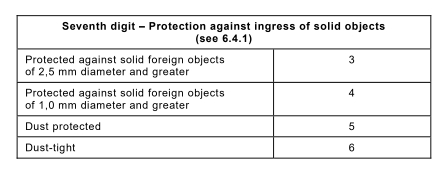
الحماية من دخول المياهتُختبر مجموعات الأنابيب، بما في ذلك التركيبات، لمقاومة الماء باستخدام أساليب IEC 60529. بالنسبة للرقمين 3 و4، يُستخدم اختبار الأنبوب المتذبذب لتقييم نفاذية الماء. تجتاز الأنظمة المصنفة بالرقم 1 فما فوق الاختبار إذا لم يُشكل تسرب الماء قطرات مرئية في الرؤية الطبيعية.
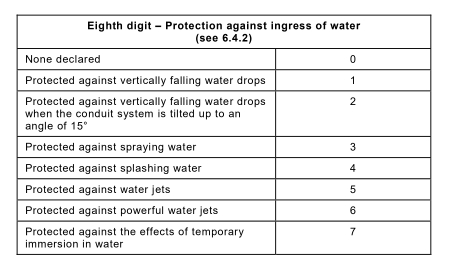
4.5.2 مقاومة التآكل
يجب أن تُظهر أنظمة الأنابيب المعدنية والمركبة، باستثناء الخيوط اللولبية، مقاومة كافية للتآكل في التطبيقات الداخلية والخارجية. تُصنف مقاومة التآكل إلى أربعة مستويات:
حماية منخفضة:الطلاءات الأساسية مثل الطلاء التمهيدي.
حماية متوسطة: مينا الموقد أو طلاء الزنك الكهربائي.
حماية متوسطة/عالية:الطلاءات المحسنة مثل Sherardizing.
حماية عالية:الطلاءات الثقيلة مثل الفولاذ المقاوم للصدأ أو طلاء الزنك بالغمس الساخن.
4.5.3 اختبار التآكل للمواد المختلفة
بالنسبة لأنظمة الأنابيب المصنوعة من الفولاذ المطلي والمطلي بالزنك والمركبة، يتم التحقق من التوافق من خلال اختبارات محددة.
حماية منخفضة:تم فحصه للتأكد من التغطية الكاملة.
حماية متوسطة:يتم تنظيفها بمذيب وغمرها في محلول يحتوي على فيري سيانيد البوتاسيوم وبيركبريتات الأمونيوم لاختبار سلامة الطلاء.
حماية عالية:تخضع لإزالة الشحوم، والغمر في حمض الكبريتيك، وكبريتات النحاس للتحقق من مقاومتها للتآكل. يجب تنظيف العينة جيدًا بعد الاختبار لإزالة أي بقايا.
ل أنابيب معدنية غير حديدية ومركبة في أنظمة مقاومة التآكل، يجب على المصنّعين تقديم معلومات حول مقاومة التآكل. قد يتم تجاهل بعض الرواسب السطحية الطفيفة، مثل ترسب النحاس على خيوط البراغي.
4.6 التوافق الكهرومغناطيسي
عادةً ما تكون المنتجات المشمولة بهذا المعيار سلبية من حيث التأثيرات الكهرومغناطيسية، بما في ذلك الانبعاث والمقاومة. هذا يعني أنه في الاستخدام العادي، لا تُصدر أنظمة التوصيل تداخلًا كهرومغناطيسيًا (EMI) ولا تتأثر بشكل كبير بالإشارات الكهرومغناطيسية الخارجية.
مع ذلك، عند تركيب هذه المنتجات كجزء من نظام أسلاك، قد يُصدر النظام بأكمله إشارات كهرومغناطيسية أو يتأثر بمجالات كهرومغناطيسية خارجية. وتعتمد درجة التأثير على طبيعة بيئة التركيب والأجهزة المتصلة بالنظام. وهذا يعني أن اعتبارات التوافق الكهرومغناطيسي (EMC) مهمة للتركيب ككل، بما في ذلك أنظمة الأنابيب.
المواد المعدنية وغير المعدنية: تنطبق متطلبات التوافق الكهرومغناطيسي (EMC) بشكل عام على أنظمة الأنابيب المعدنية وغير المعدنية. ومع ذلك، قد توفر الأنابيب المعدنية حماية أفضل ضد التداخل الكهرومغناطيسي مقارنةً بالأنابيب غير المعدنية، التي تُعتبر أكثر سلبية من حيث الانبعاثات الكهرومغناطيسية والحماية.
5. الأنابيب المعدنية مقابل الأنابيب البلاستيكية غير المعدنية
انتهينا من شرح معيار IEC 61386-1. بفهم الاختبارات والتصنيفات المختلفة الموضحة في المعيار، يمكنك اتخاذ قرار مدروس بين مواد مختلفة، مثل أنابيب الكهرباء المصنوعة من مادة PVC غير المعدنية وأنظمة الأنابيب المعدنية.
فيما يلي، سوف نقدم لك معلومات أكثر تفصيلاً عن الأنابيب المعدنية والأنابيب البلاستيكية لمساعدتك على فهم أفضل.
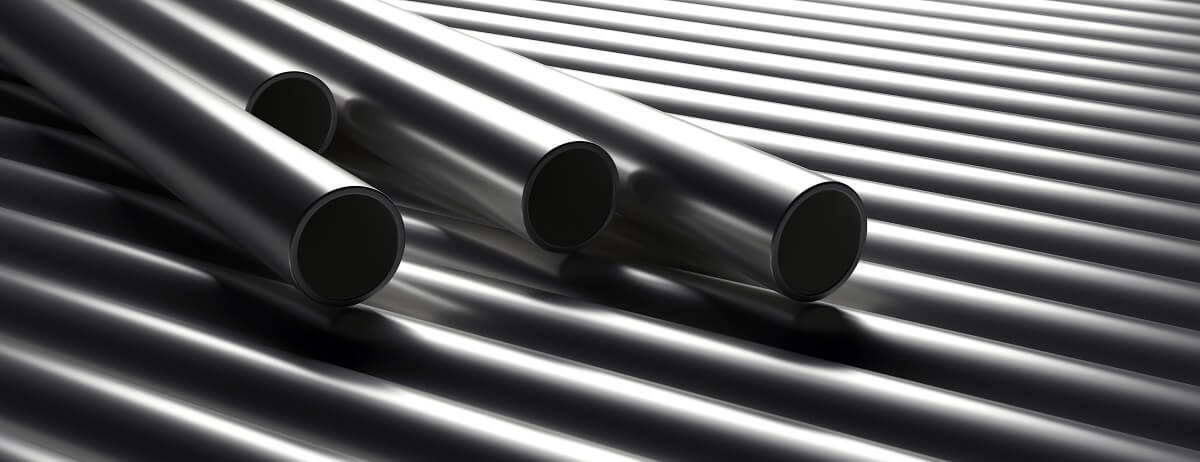
5.1 الأنابيب المعدنية
من خلال الاختبارات والمتطلبات المذكورة أعلاه والموضحة في معيار IEC 61386-1، يمكننا فهم مزايا وعيوب أنظمة الأنابيب المعدنية، بالإضافة إلى أنواعها المختلفة المتاحة. تُبرز هذه الاختبارات عوامل رئيسية، مثل المتانة الميكانيكية، ومقاومة الحريق، والحماية الكهرومغناطيسية، وهي مزايا مهمة للأنابيب المعدنية.
ومع ذلك، فإنها تكشف أيضًا عن تحديات مثل الوزن، وتعقيد التركيب، والقابلية للتآكل.
وفيما يلي، نقدم لك ملخصًا لفهمك بشكل أفضل.
5.1.1 أنواع الأنابيب المعدنية
القناة المعدنية الصلبة (RMC) أنبوب فولاذي سميك الجدران، مصمم لتوفير أقصى حماية في التطبيقات الصناعية والتجارية. يتميز بمتانته العالية، ولكنه ثقيل الوزن ويتطلب استخدام الخيوط لتوصيلاته.
القناة المعدنية المتوسطة (IMC) بديل أخف وزنًا لـ RMC، يوفر حماية جيدة ووزنًا أخف. يُستخدم عادةً في الأماكن الخارجية والصناعية.
الأنابيب المعدنية الكهربائية (EMT) أنبوب فولاذي خفيف الوزن، رقيق الجدران، سهل التركيب والثني، مما يجعله مثاليًا للمباني التجارية والتطبيقات الداخلية. مع ذلك، يوفر حماية ميكانيكية أقل من أنابيب RMC أو IMC.
قناة معدنية مرنة (FMC) - تم تصميم FMC للتطبيقات التي تتطلب المرونة، ويتم استخدامه في المناطق التي تشكل فيها الحركة أو الاهتزاز مصدر قلق، مثل توصيلات المحرك.
قناة معدنية مرنة سائلة (LFMC) - مشابه لـ FMC ولكنه مغطى بطبقة بلاستيكية مقاومة للماء، مما يجعله مناسبًا للبيئات الرطبة أو الخارجية.
أنابيب الألومنيوم - بديل مقاوم للتآكل للأنابيب الفولاذية، ويُستخدم غالبًا في البيئات التي تشكل الرطوبة فيها مصدر قلق، مثل المناطق الساحلية.
5.1.2 الطلاءات الواقية للأنابيب المعدنية
لتعزيز المتانة ومقاومة التآكل، غالبًا ما تُعالج الأنابيب المعدنية بطلاءات واقية. بعضها مصنوع من مواد مركبة.
طلاء مجلفن - يتم تطبيقه على الأنابيب الفولاذية لمنع الصدأ والتآكل، وعادة ما يتم ذلك باستخدام الجلفنة بالغمس الساخن.
طلاء الإيبوكسي - يوفر حماية إضافية ضد المواد الكيميائية والبيئات القاسية، ويستخدم عادة في البيئات الصناعية.
طلاء البولي فينيل كلوريد - يضيف طبقة إضافية من العزل ومقاومة التآكل، مما يجعله مناسبًا للتركيبات تحت الأرض والخارجية.
الألومنيوم المؤكسد - يحسن مقاومة أنابيب الألومنيوم للأكسدة، مما يجعلها مثالية للبيئات البحرية والرطبة.
5.1.3 مزايا وعيوب الأنابيب المعدنية
المزايا:
حماية ميكانيكية ممتازة للأسلاك الكهربائية.
مقاومة عالية للحريق والأضرار المادية.
يوفر حماية كهرومغناطيسية للأنظمة الكهربائية الحساسة.
مناسب للبيئات القاسية والصناعية.
العيوب:
أثقل وزنًا وأكثر صعوبة في التثبيت مقارنة بالأنابيب غير المعدنية.
عرضة للتآكل إذا لم يتم طلائها أو صيانتها بشكل صحيح.
يتطلب التأريض، مما يضيف تعقيدًا إلى التثبيت.
5.1.4 التطبيقات الشائعة للأنابيب المعدنية
المرافق الصناعية - يحمي الأسلاك في المصانع والمنشآت.
المباني التجارية - تستخدم غالبًا في المساحات المكتبية ومتاجر البيع بالتجزئة.
المواقع الخطرة - مناسب للبيئات المتفجرة أو عالية الخطورة.
التركيبات الخارجية - يتم استخدام RMC وIMC بشكل شائع في الأماكن المكشوفة.
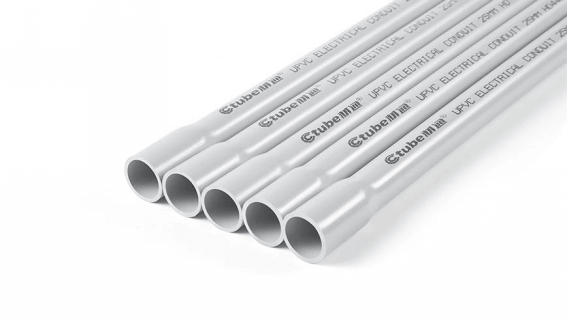
5.2 أنابيب PVC
أنابيب PVC (كلوريد البوليفينيل) هي بديل غير معدني شائع الاستخدام للأنابيب المعدنية، وتتميز بمزايا عديدة، منها مقاومة التآكل وخفة الوزن وسهولة التركيب. على عكس الأنابيب المعدنية، لا توصل أنابيب PVC الكهرباء، مما يُغني عن التأريض. هذا يجعلها الخيار الأمثل للتطبيقات السكنية والتجارية وتحت الأرض. نستعرض أدناه أنواع أنابيب PVC وفوائدها وعيوبها المحتملة.
5.2.1 أنواع أنابيب PVC/الأنواع الخاصة
أنابيب PVC الصلبة (RPVC) أنبوب متين ذو جدران سميكة، مصمم للاستخدامات تحت الأرض وفي الأماكن المكشوفة. يتميز بمقاومته للصدمات والرطوبة، ويُستخدم عادةً في الدفن المباشر والأماكن الرطبة.
الأنابيب الكهربائية غير المعدنية (ENT) أنبوب مرن ومموج من مادة PVC، خفيف الوزن وسهل الثني. يُستخدم بشكل رئيسي في التطبيقات الداخلية التي تتطلب تركيبًا سريعًا وبسيطًا.
أنابيب الطاقة الشمسية UPVC أنبوب مقاوم للأشعة فوق البنفسجية ومقاوم للعوامل الجوية، مصمم خصيصًا لتركيبات الألواح الشمسية. يحمي الأسلاك من التعرض الطويل لأشعة الشمس، ودرجات الحرارة القصوى، والظروف الخارجية القاسية، مما يضمن أداءً طويل الأمد في أنظمة الطاقة المتجددة.
أنابيب LSZH البلاستيكية منخفضة الدخان وخالية من الهالوجين أنبوب مُصمم خصيصًا للبيئات المغلقة، مثل الأنفاق والمباني التجارية وأنظمة النقل العام. يُقلل هذا الأنبوب من انبعاثات الدخان السام والهالوجين في حالة الحريق، مما يُقلل من المخاطر الصحية وتلف المعدات.
5.2.2 مزايا وعيوب أنابيب PVC
المزايا:
مقاومة التآكل والمواد الكيميائية - على عكس الأنابيب المعدنية، لا يصدأ أو يتآكل البولي فينيل كلوريد (PVC)، مما يجعله مثاليًا للبيئات الرطبة والمسببة للتآكل.
خفيفة الوزن وسهلة التركيب – مادة PVC أخف وزنًا بكثير من الأنابيب المعدنية، مما يقلل من تكاليف العمالة والنقل. ويمكن قطعها وتجميعها بسهولة باستخدام مادة لاصقة مذيبة.
العزل الكهربائي - نظرًا لأن مادة PVC غير موصلة، فهي لا تتطلب التأريض، مما يسهل عملية التركيب.
مقاومة الطقس والأشعة فوق البنفسجية - بعض أنواع قنوات PVC مقاومة للأشعة فوق البنفسجية، مما يجعلها مناسبة للتطبيقات الخارجية.
فعاله من حيث التكلفه - بشكل عام أكثر تكلفة من الأنابيب المعدنية، مما يجعلها خيارًا صديقًا للميزانية لمختلف التركيبات الكهربائية.
العيوب:
قوة ميكانيكية أقل - لا يعد البولي فينيل كلوريد مقاومًا للصدمات مثل الأنابيب المعدنية، مما يجعله أقل ملاءمة للمناطق ذات الضغط الميكانيكي العالي.
مقاومة محدودة لدرجات الحرارة العالية – يمكن أن يتشوه أو يتحلل البولي فينيل كلوريد (PVC) تحت تأثير الحرارة الشديدة، مما يحد من استخدامه في البيئات ذات درجات الحرارة العالية.
التوسع والانكماش – يتمدد ويتقلص البولي فينيل كلوريد مع تغيرات درجات الحرارة، مما يتطلب وصلات تمدد في بعض التركيبات.
5.2.3 التطبيقات الشائعة لأنابيب PVC
الأسلاك السكنية - يستخدم في المنازل لحماية الكابلات الكهربائية في الجدران والأسقف والأرضيات.
المنشآت التجارية - مثالي للمباني المكتبية ومساحات البيع بالتجزئة والمستودعات حيث يفضل استخدام الحماية غير المعدنية.
أنظمة تحت الأرض - يستخدم بشكل متكرر في الخطوط الكهربائية المدفونة بسبب مقاومته للرطوبة.
البيئات الرطبة والتآكلية - مناسب للإعدادات الصناعية المعرضة للمواد الكيميائية أو الرطوبة العالية.
مشاريع الطاقة المتجددة - يتم استخدامه في تركيبات الطاقة الشمسية وطاقة الرياح لحماية الأسلاك بكفاءة وطويلة الأمد.
6. الخاتمة
لا يقتصر الاختيار بين الأنابيب الكهربائية المعدنية والبلاستيكية على تحديد المادة الأفضل فحسب، بل يعتمد على عوامل متعددة، منها الامتثال لمعايير الصناعة، والمتطلبات الخاصة بالمشروع، وقيود الميزانية، والظروف البيئية. لكل نوع من الأنابيب مزاياه وتطبيقاته المثالية.
نأمل أن تكون هذه المقالة قد قدمت رؤى قيمة لمساعدتك في اتخاذ قرار مستنير عند اختيار حلول الأنابيب الكهربائية لاحتياجاتك.
عن كتوب
Ctube شركة رائدة في مجال تصنيع قنوات الكابلات البلاستيكية (PVC)، بخبرة تزيد عن عشر سنوات. نتخصص في توفير حلول عالية الجودة لقنوات الكهرباء، مع ضمان المتانة والسلامة والامتثال للمعايير الدولية. قنواتنا القياسية AS/NZS 2053 وقنوات الأسلاك منخفضة الدخان وخالية من الهالوجين (LSZH) تلبي معايير IEC، وتحمل الشهادات اللازمة، وخضعت لاختبارات دقيقة من قِبل
مختبرات الطرف الثالث.
إذا كنت مهتمًا بمعرفة المزيد عن منتجاتنا أو تحتاج إلى إرشادات لاختيار الأنبوب المناسب، فلا تتردد في التواصل معنا. شكرًا لقراءتك!