Tubería de PVC vs. Conducto de PVC: La guía comparativa definitiva (2025)
1. Introducción
PVC pipes and PVC conduits are often confused due to their similar appearance, but they serve entirely different purposes in construction. PVC pipes are primarily used for drinking water transmission, drainage, waste, and vent (DWV) systems, as well as irrigation.
In contrast, PVC conduits are designed to protect electrical wiring in residential, commercial, and industrial settings.
Their differences go beyond just application—factors such as material composition, structural design, color coding, fittings, adhesives, and regulatory standards set them apart. In this post, we’ll break down these key differences, explain why distinguish these pipe types important.
2. Material Composition and Manufacturing Between PVC Pipe and PVC Conduit
2.1 Base Polymer Formulation
The foundational chemistry of PVC pipe and conduit begins with polyvinyl chloride (PVC) resin, a thermoplastic polymer synthesized from vinyl chloride monomers. While both products share the same base polymer, their resin grades and molecular structures differ significantly to meet distinct performance requirements.
The ASTM D1784 standard defines the specifications for rigid Polyvinyl Chloride (PVC) and Chlorinated Polyvinyl Chloride (CPVC) compounds used in various applications, including extruded and molded products. These materials are particularly valued for their chemical resistance, heat resistance, and durability, making them ideal for piping systems and other industrial applications.
Composition and Properties
PVC and CPVC compounds covered under ASTM D1784 primarily consist of:
- Polyvinyl chloride (PVC)
- Chlorinated polyvinyl chloride (CPVC)
- Vinyl chloride copolymers (with at least 80% vinyl chloride content)
PVC Pipe:
PVC pipes are manufactured using polyvinyl chloride (PVC) plastics that meet strict quality and safety standards. These materials are categorized based on two key strength tests: Short-term strength tests and Long-term strength tests.
The compounds used in PVC pipes must conform to ASTM D1784 classifications, specifically:
PVC 12454 – Offers high strength and impact resistance.
PVC 14333 – Provides enhanced durability and performance.
The certification process must follow NSF/ANSI Standard No. 14, which sets guidelines for plastic piping systems used in water distribution. Certified pipes should bear the seal or mark of the testing laboratory to confirm compliance. Additionally, pipes designed for reclaimed water systems must meet specific marking requirements.
Conducto de PVC
The PVC conduit must be made from virgin homopolymer PVC compounds, classified under ASTM D1784. These compounds fall into the following categories:
12254 or 121643 – Requires a minimum tensile strength of 4,000 psi (28 MPa).
12264 – Requires a minimum tensile modulus of 500,000 psi, providing enhanced rigidity.
In addition to conduits, molded fittings are manufactured using PVC compounds with a cell classification of 12234 or 13343, also in accordance with ASTM D1784.
Maybe some confusion will arise fot the classification like 12254 we mentioned above, here we make a brief introduce.
Classification System Overview
ASTM D1784 categorizes PVC and CPVC compounds using a cell-based numbering system. This system assigns a numerical code to each material based on its key properties, allowing for easy comparison and selection. The classification covers:
- Impact resistance (ability to withstand force without breaking)
- Tensile strength (resistance to pulling forces)
- Modulus of elasticity (stiffness and flexibility)
- Deflection temperature under load (heat resistance)
- Hydrostatic design basis (pressure endurance over time)
The classification table in ASTM D1784 (Table 1) organizes materials into different performance levels. Each property is assigned a range, and a compound must meet the minimum value in each category to receive a classification.
For example, a PVC compound with the classification 12454 can be broken down as follows:
- 1: Base resin type – Polyvinyl chloride (PVC)
- 2: Impact resistance – Moderate level (40 ft-lbf/in or 0.65 J/m)
- 4: Tensile strength – Minimum 7000 psi (48 MPa)
- 5: Modulus of elasticity – Minimum 400,000 psi (2760 MPa)
- 4: Deflection temperature – 100°C (212°F)
Each digit in the classification number represents a different property category, making it easy to compare materials at a glance.
While ASTM D1784 provides a general classification system, selecting the right compound requires consideration of additional factors such as:
- Application-specific requirements (e.g., underground conduit vs. potable water pipes)
- Environmental conditions (e.g., UV exposure, temperature variations)
- Compliance with industry regulations (e.g., NSF/ANSI 14 for potable water)
Therefore, whether you are purchasing electrical conduits or water pipes, it is essential to verify the raw materials with the supplier to ensure they meet the specific requirements of your project.
Due to space limitations, we are providing only a brief introduction here. For more detailed information, you can refer to the original text. We have included the reference sources at the end of this article.
2.2 Critical Additives Comparison
According to ASTM D 1784, in addition to the PVC raw materials we have mentioned above, there will be some compounding ingredients consist of lubricants, stabilizers, non-poly(vinylchloride) resin modifiers, pigments, and inorganic fillers to produce the PVC pipe and PVC conduit. And in this part, we call additives. These additives determine the product’s strength, flexibility, UV resistance, and fire-retardant capabilities. This is one of the difference between PVC pipe and PVC conduit.
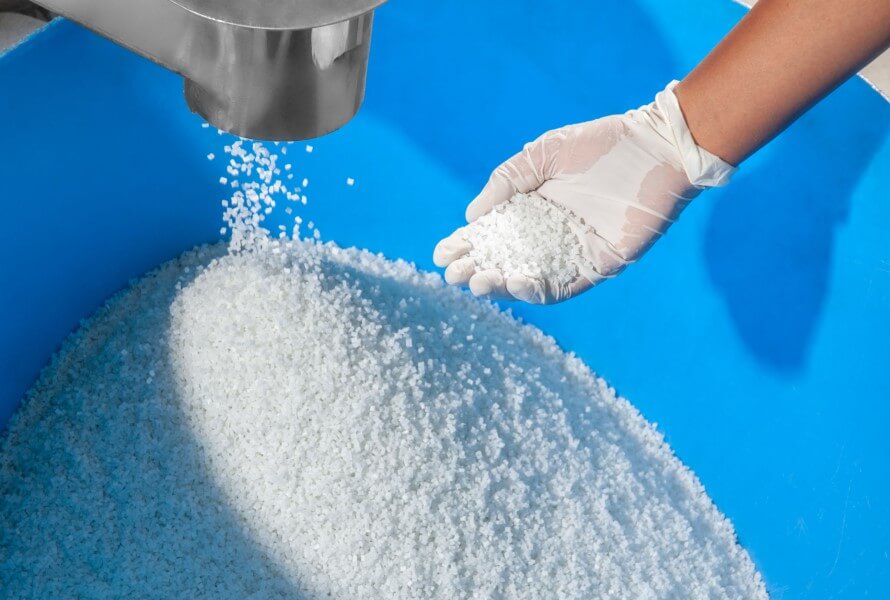
2.2.2 Role of UV Inhibitors
Titanium Dioxide (TiO₂) is the primary UV stabilizer, acting as a protective barrier to prevent photodegradation.
PVC Pipe, especially potable water and DWV (Drain, Waste, Vent) applications, is usually buried or installed indoors, reducing the need for UV inhibitors.
Some pressure-rated PVC pipes used for outdoor irrigation or water mains may contain low levels of UV stabilizers, but they are not as extensive as those in electrical conduit.
PVC Conduit requires enhanced UV resistance especiallyinstalled above ground, where prolonged sun exposure can cause embrittlement and surface degradation.
2.2.3 Role of Flame Retardancy
Antimony Trioxide (Sb₂O₃) and Halogenated Compounds are generally added as fire retardants to prevent flame spread in electrical conduit.
PVC Pipe is not required to have flame retardants because it is designed only for fluid transmission.
PVC Conduit is required by the National Electrical Code and UL or other national electrical safety requirements to be flame-resistant and self-extinguishing.
Famous requirements is UL 94 V-0 rating ensures that PVC conduit self-extinguishes within 10 seconds after flame exposure.
- Unión Europea (UE): Bans certain phthalates in food and water contact applications under REACH (Regulation EC 1907/2006).
- United States (EPA & FDA): Regulates plasticizers in drinking water pipes, requiring compliance with NSF/ANSI 61 standards。
- Porcelana: Bans specific phthalates in food and drinking water applications.
- Japan: Prohibits the use of DEHP and similar plasticizers in potable water systems.
2.2.5 Role of Antimicrobial Additives
Antimicrobial additives are chemical compounds incorporated into PVC materials to inhibit the growth of bacteria, mold, fungi, and algae. These additives help maintain hygienic conditions and prevent biofilm formation. Common types such as Silver ions (Ag⁺), Zinc-based compounds, Triclosan alternatives.
PVC Pipe: Prevents microbial-induced degradation in sewage and drainage pipes to extend pipe lifespan. And ensures potable water remains safe for human consumption.
While antimicrobial additives are not used in PVC Conduit for electrical conduits do not transport fluids and they are primary focus is fire resistance, UV stability, and mechanical strength.
3. Structural Design Differences Between PVC Pipe and PVC Conduit
Now that we have explored the differences in raw materials and additives used in PVC pipes and conduits, it is equally important to examine their structural and design variations. While both products may appear similar at first glance, their wall thickness, strength, pressure ratings, and color coding are specifically tailored to their intended applications.
In the following sections, we will break down these key structural distinctions to help you better understand their functionality and proper usage.
3.1 Wall Thickness and Strength
One of the most fundamental differences between PVC pipes and PVC conduits lies in their wall thickness and structural strength. These variations are driven by their intended applications.
PVC pipes must withstand internal water pressure, while PVC conduits are designed to protect electrical wiring without carrying fluids. So internal pressure resistance is unnecessary. They focus on withstanding impact and crushing forces from outside.
The equation: 2𝑆/𝑃 = (D₀/𝑡)−1
- S (Hydrostatic Design Stress): Measured in psi (or MPa).
- P (Pressure Rating): Also measured in psi (or MPa).
- D₀ (Average Outside Diameter): Given in inches or millimeters, this is the external diameter of the pipe, which directly influences its pressure capacity.
- t (Minimum Wall Thickness): Measured in inches or millimeters, this represents the thinnest allowable section of the pipe wall, ensuring structural integrity under pressure.
This formula helps engineers and manufacturers determine the appropriate pipe dimensions needed for specific pressure requirements.
And there are also some some essential tests used in ASTM and other standards to assess PVC pipe performance.
Sustained Pressure Test: This test ensures that the pipe can sustain high water pressure over time, preventing leaks or bursts in plumbing systems.
Accelerated Regression Test: This test predicts the long-term water pressure resistance and service life of the PVC pipe.
Burst Pressure Test: Determines the maximum internal pressure the pipe can withstand before bursting.
Flattening Test: Evaluates the mechanical strength and flexibility of the PVC pipe under external compression. This test ensures the pipe can withstand soil pressure, heavy loads, and physical impacts during installation and service.
3.1.2 Key Terms and Performance Tests of PVC Conduit
When selecting PVC electrical conduit, there are some several key factors that the buyer maybe focus on. Critical aspects include wall thickness, outer and inner diameter, wall thickness as well as wire fill capacity.
Outer Diameter (OD): Defines the conduit’s total width, affecting installation compatibility with fittings and supports.
Inner Diameter (ID): Determines how many electrical wires can be safely routed inside the conduit. The available space inside the conduit must comply with wire fill regulations.
Espesor de la pared: Affects mechanical strength, impact resistance, and environmental durability. It is also crucial for inner space calculations.
Wire Fill Capacity: Refers to the maximum number and size of electrical conductors that can be safely installed inside a conduit without causing overheating or excessive resistance.
NEC Guidelines for Conduit Fill
The NEC provides specific guidelines for maximum wire fill percentage based on the number of conductors inside a conduit:
- 1 wire: Up to 53% of the conduit’s internal area can be filled.
- 2 wires: Up to 31% of the internal area.
- 3 or more wires: The total fill should not exceed 40% of the internal area.
Conduit fill tables help electricians choose the right conduit size for a specific number of conductors.
When evaluating the strength and mechanical performance of PVC electrical conduit, industry standards rely on specific tests and measured data to ensure durability and compliance. Key assessments include:
Resistencia al impacto: PVC conduit must withstand mechanical impact per UL 651, ensuring it does not crack or break under normal installation conditions.
Resistencia a la tracción: This measures how much pulling force the conduit can endure before breaking.
Resistencia al aplastamiento: Indicates how much external pressure (e.g., from soil, concrete, or heavy loads) the conduit can withstand without deforming.
Deflection Testing: This evaluates how much a conduit can bend under pressure before permanent deformation occurs.
3.2 Understanding Schedule and Pressure Ratings in PVC Pipe and PVC Conduit
In our earlier discussion on PVC water pipes, we introduced the concept of pressure rating, which is a critical factor in determining a pipe’s ability to withstand internal water pressure. This concept is widely used for water pipes but is less commonly applied to electrical conduit since conduits are not designed to carry pressurized fluids.
3.2.1 Schedule of PVC Pipe and PVC Conduit
However, when it comes to the Schedule (Sch) classification, this is a system frequently encountered in both PVC water pipes and electrical conduits.
The Schedule (Sch) classification refers to the wall thickness of a PVC pipe or conduit relative to its nominal size. It is a standardized system primarily used in North America, with common classifications including Anexo 40 (Sch 40) and Anexo 80 (Sch 80).
The higher the Schedule number, the thicker the pipe wall. For example, Sch 80 pipes have thicker walls than Sch 40 pipes of the same nominal size, making them stronger and more resistant to pressure.
3.2.2 SDR in PVC Pipe
PVC pipes are classified using both SDR and Schedule (Sch) ratings, but they follow different methodologies. While PVC conduit do not use SDR.
SDR (Standard Dimension Ratio) is a key parameter used to define the relationship between a PVC pipe’s outer diameter (OD) and wall thickness. It is an essential factor in determining the pressure rating of the pipe. SDR pipes maintain a consistent OD-to-wall thickness ratio, meaning that wall thickness increases proportionally with pipe size while maintaining the same pressure rating.
The formula for SDR is: SDR=Outer Diameter (OD) / Wall Thickness
Lower SDR values indicate thicker walls and higher pressure resistance.
Higher SDR values mean thinner walls and lower pressure resistance.
As the Table 2 showing.
3.3 Color Coding and Identification in PVC Pipe and PVC Conduit
Color coding plays an essential role in differentiating PVC pipes and conduits, helping users quickly identify their intended applications.
It’s important to note that the color variations can depend on regional standards, but these general guidelines help distinguish pipe functions at a glance.
PVC pipe usually use white for water supply and drain, waste, and vent (DWV) systems.
And Gray is the most common color for standard electrical conduit.
3.3.1 Standard Color Coding for PVC Pipes
PVC pipes used in plumbing, irrigation, and industrial applications often follow these general color conventions:
- White or Gray – Commonly used for potable (drinking) water supply and drain, waste, and ed (non-potable) water for irrigation and industrial reuse.
- Orange or Red – Used in fire suppression systems (e.g., underground fire mains).
3.3.2 Standard Color Coding for PVC Conduits
Electrical PVC conduits follow a different set of color conventions, mainly dictated by industry standards and electrical codes:
- Gris – The most common color for standard electrical conduit, including Schedule 40 and Schedule 80 PVC conduits used in residential, commercial, and industrial wiring.
- Orange or Red – Often used for high-voltage or underground electrical lines to signal caution during excavation.
- Blue or White – Frequently designated for communication cables, fiber optic lines, and low-voltage applications.
However, the actual color of PVC conduit may vary depending on specific applications and manufacturer preferences. The colors listed above serve as general guidelines, but local electrical installation codes and regulations should always be referenced to ensure compliance with regional requirements.
3.3.3 Markings and Identification Labels
PVC pipes and conduits are typically marked with essential information to help users identify their intended application, compliance with industry standards, and key specifications. These markings ensure proper selection and installation based on safety and regulatory requirements.
Below are the common elements found on PVC pipe and conduit markings:
- Manufacturer Name or Code: Identifies the producer of the pipe or conduit.
- Production Date and Batch Code: Used for quality control and traceability in case of defects or recalls.
- Pipe Size and Dimensions: Clearly indicates nominal pipe size (NPS) or outer diameter (OD) to ensure correct selection and compatibility.
- Material Designation: Labeled with “PVC” followed by the material grade (e.g., “PVC 1120” or “PVC 1220”).
- Schedule (SCH): Common for both plumbing and conduit, indicating wall thickness classifications such as “SCH 40” or “SCH 80.”
4. Comparison of Connection Methods in PVC Pipe and Conduit
Besides the differences in materials, concepts, structure, and color that we have discussed, PVC water pipes and electrical conduits also differ significantly in their fittings and connection methods.
These variations are essential to ensure proper functionality in their respective applications—water pipes require leak-proof joints to withstand pressure, while electrical conduits need secure yet accessible connections for wire installation and maintenance.
In the following section, we will explore the differences in fittings, bends, and joining techniques used for PVC pipes and conduits.
4.1 Functions and Roles of Fittings in PVC Pipe and Conduit
Fittings are essential components in both PVC piping and conduit systems, such as
Connecting Sections: Coupling-Joining two or more pieces of pipe or conduit together to extend the system.
Changing Direction: Elbow-Allowing smooth transitions at various angles to navigate obstacles or align with design requirements.
Branching the System: Tee- Creating multiple pathways for fluid flow (in plumbing) or wire routing (in electrical applications).
Sealing and Protection: Ensuring leak-proof water distribution for plumbing and secure, insulated connections for electrical conduits.
4.2 Different Fittings Requirements in PVC Pipe and Conduit
One key difference between the two systems is the need for junction boxes and adaptable boxes in electrical conduit systems, which are not found in water piping.
Junction Boxes act as interconnection points for electrical wires, providing space for splicing and ensuring safety.
Adaptable Boxes allow flexibility in conduit design, making it easier to modify or expand electrical systems.
These enclosures also provide mechanical protection for electrical connections, preventing exposure to moisture, dust, and external damage.
Another biggest difference is the requirement about the bending and turning.
There are no strict regulations on total bend angles in a PVC water pipe system, as long as flow efficiency is maintained.
But in electrical conduit installation, NEC (National Electrical Code) limits the total bends between pull points to 360° to prevent excessive wire friction. If more bends are needed, a junction box or pull box must be installed. The requirement ensure wires can be pulled through the conduit without excessive friction or damage.
4.3 Solvent Cement (Glue) Welding in PVC Pipe and PVC Conduit
Solvent cement is a type of adhesive specifically designed for bonding PVC pipes and fittings by chemically softening the material to create a strong, permanent connection.
Solvent cement does not just stick surfaces together—it fuses them into a single, continuous piece. This bonding method ensures a durable and leak-proof joint, making it widely used in both plumbing and electrical conduit installations.
However, different types of solvent cement are formulated for water pipes and electrical conduits, each with unique properties suited to their specific applications.
Acccording to ASTM D2564-20 (Reapproved 2024), Standard Specification forSolvent Cements for Poly(Vinyl Chloride)(PVC) Plastic Piping Systems, there some requirements have to follow.
Resin Content: The PVC resin content must be at least 10%.
Dissolution Ability: The cement must be able to dissolve an additional 3% by weight of PVC 12454-B compound (either powder or granular) or an equivalent PVC resin at 73.4 ± 3.6°F (23 ± 2°C) without signs of gelation.
Cements are categorized into three types based on their minimum viscosity:
- ≥ 250 psi (1.7 MPa) after 2 hours of curing
- ≥ 500 psi (3.4 MPa) after 16 hours of curing
- ≥ 900 psi (6.2 MPa) after 72 hours of curing
Hydrostatic Burst Strength: The minimum hydrostatic burst strength must be ≥ 400 psi (2.8 MPa) after 2 hours of curing.
While Hydrostatic Burst Strength do not require hydrostatic testing since they are not designed for liquid transport.
Generally speaking, plumbing-grade solvent cement must meet potable water safety standards, ensuring no harmful chemicals leach into drinking water. Electrical conduit solvent cement is formulated for durability and water resistance, as it is often used in environments where electrical safety is a concern.
When purchasing PVC solvent cement, always confirm with your supplier whether it is intended for water pipes or electrical conduits. Some solvent cements are interchangeable, while others are specifically formulated for one application due to differences in resin content, viscosity, and bonding strength. Always check the formulation requirements to ensure compatibility with your intended use.
5. Code Compliance and Standards: Differences Between Water Pipes and Electrical Conduits
Both PVC water pipes and PVC electrical conduits must comply with specific regulations and industry standards to ensure safety, performance, and durability. However, the standards governing these two types of pipes differ significantly based on their intended applications. In the following, we make some examples as USA and Canada, but remember have to follow the local regulations.
5.1 Water PVC Pipe Regulations
PVC water pipes are primarily regulated by plumbing and water quality standards to ensure they can handle pressurized water safely without leaching harmful substances.
- NSF/ANSI 61 – Ensures the pipe is safe for potable water。
- ASTM International (ASTM D1785, D2241, etc.) – Sets material and performance standards.
- American Water Works Association (AWWA C900, C905) – Governs large-diameter water pipes.
- ISO 1452 – International standard for PVC-U pressure pipes.
5.2 Electrical Conduit Regulations
PVC electrical conduits must comply with electrical safety codes to ensure they provide adequate protection for wiring, resistance to environmental factors, and mechanical strength.
- UL (Underwriters Laboratories, UL 651,1653) – Certifies electrical conduits for safety and fire resistance.
- National Electrical Code (NEC, NFPA 70) – Sets installation requirements.
- National Electrical Manufacturers Association (NEMA TC-2, TC-3) – Defines conduit properties.
- CSA (Canadian Standards Association, C22.2 No. 211.1) – Governs electrical conduit standards in Canada.
6. Conclusión
PVC pipes and conduits are both made from PVC, but they differ in structural design, material composition, and application. Pipes are designed primarily for carrying fluids and gases, while conduits are engineered to protect electrical wiring.
For professionals and DIY enthusiasts, it is crucial to choose PVC pipes or conduits based on their intended purpose. Electricians should prioritize conduits for electrical wiring installations, ensuring compliance with relevant standards for safety and longevity. Plumbers should use PVC pipes designed for fluid systems. Always follow the manufacturer’s guidelines, and make sure to select the correct fittings and adhesives to guarantee the quality and durability of the installation.
Ctube is a trusted electrical conduit supplier, offering a wide range of high-quality CLORURO DE POLIVINILO, UPVC, y LSZH conduits. Our products are designed to meet the demands of various electrical applications, providing exceptional durability, safety, and performance. Whether you’re working on a residential, commercial, or industrial project, Ctube offers the right conduit solutions to ensure secure and long-lasting installations.
Thanks for your reading, and good luck with your project.
Reference
- ASTM D 4396 Standard Specification for Rigid Poly(Vinyl Chloride)(PVC) and Chlorinated Poly(Vinyl Chloride)(CPVC) Compounds for Plastic Pipe and Fittings Used in Nonpressure Applications
- ASTM D 3915 Standard Specification for Rigid Poly(Vinyl Chloride) (PVC) and Chlorinated Poly (VinylChloride) (CPVC)Compounds for Plastic Pipe and Fittings Used in Pressure Applications1
- ASTM D 2241 Standard Specification for Poly(Vinyl Chloride)(PVC) Pressure-Rated Pipe (SDR Series)
- ASTM D 1784 Standard Specification for Rigid Poly(Vinyl Chloride)(PVC) Compounds and Chlorinated Poly(Vinyl Chloride)(CPVC) Compounds
- ASTM D 2665 Standard Specification for Poly(Vinyl Chloride)(PVC) Plastic Drain, Waste, and Vent Pipe and Fittings
- ASTM F512-12 Standard Specification for Smooth-Wall Poly(Vinyl Chloride)(PVC) Conduit and Fittings for Underground Installation
- ASTM D1785-21a Standard Specification for Poly(Vinyl Chloride)(PVC) Plastic Pipe, Schedules 40, 80 and 120
- ASTM D4216 Standard Specification for Rigid Poly(Vinyl Chloride) (PVC) and Related PVC and Chlorinated Poly(Vinyl Chloride)(CPVC) Building Products Compounds
- ASTM D2122 Standard Test Method for Determining Dimensions of Thermoplastic Pipe and Fittings
- ASTM D1785 Standard Specification for Poly(Vinyl Chloride)(PVC) Plastic Pipe, Schedules 40, 80,and 1201
- ASTM D2564-20 Standard Specification for Solvent Cements for Poly(Vinyl Chloride) (PVC) Plastic Piping Systems
- ASTM F493-20 Standard Specification for Solvent Cements for Chlorinated Poly(Vinyl Chloride) (CPVC) Plastic Pipe and Fittings
- ASTM D3138-21 Standard Specification for Solvent Cements for Transition Joints Between Acrylonitrile-Butadiene-Styrene (ABS) and Poly(Vinyl Chloride) (PVC) Non-Pressure Piping Components
- ASTM D2855-20 Standard Practice for the Two-Step (Primer and Solvent Cement) Method of Joining Poly (Vinyl chloride) (PVC) or chlorinated Poly(Vinyl Chloride)(CPVC) Pipe and Piping components with Tapered Sockets
- ASTM F656-21 Standard Specification for Primers for Use in Solvent Cement Joints of Poly (VinylChloride) (PVC) Plastic Pipe and Fittings
Tubería de PVC vs. Conducto de PVC: La guía comparativa definitiva (2025) Leer más "